Gas Cooling in India
Spray Nozzles Online has decades of experiences providing gas cooling solutions for corporations worldwide in India.
We are engaged in offering the wide range of Gas Cooling Systems in India. Our products are manufactured using latest techniques and superior quality material. We offer effective and technically advanced Gas Cooling Systems to our patrons. These systems are available as per the industry standards and used in various industries. Spray Nozzles Online offers gas cooling systems for various applications that can be individually adapted to customers’ requirements. Best results are achieved in gas cooling processes only when detailed knowledge of the process-specific requirements is available to assist in the choice of nozzles. The cooling of gas flows by infusing water or different coolants is an exceptionally normal application for our spray nozzles. Right nozzle choice is of basic significance in many spray cooling applications as the properties of the spray will decide how rapidly heat is assimilated and where the spray will reach inside a given gas flow.
Types
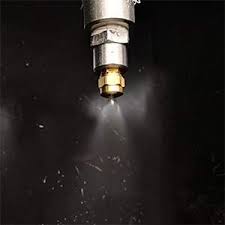
Air Inlet Cooling-Air Atomizing Nozzles
Many facilities or processes in hot, dry areas can benefit from using spray nozzles to cool the inlet air streams. Evaporating water into the inlet air can provide critical cooling of heat sensitive areas such as electronic server rooms or animal enclosures. It can also provide significant increases in the efficiency of equipment such as gas turbines or air-cooled condensers by cooling the air and increasing the relative humidity level of the inlet air streams to these units. Spray nozzles can provide an effective and economical alternative to the use of electric chillers in many applications.
Important factors to consider
- Air temperature & humidity
- Available quench length
- Available/required flow rate
- The available pressure drop across the nozzle
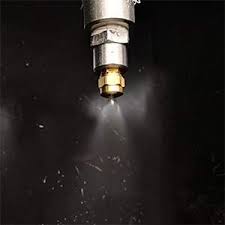
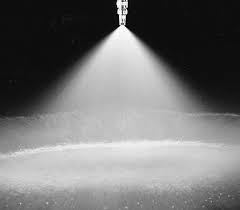
Cooling Deluge-Full Cone Nozzles
Spray Nozzles Online provides a range of high-quality nozzles that are useful for reducing the temperature of various components and parts using a deluge spray. Many production processes require the product to be hot during work and then cooled back to ambient temperature. In metal processing industries, castings, extrusions, and hot-worked products fall into this category, as do any components that have been heated treated. In the food industry, many products are packaged hot and must be cooled before storage and shipment. Regardless of whether you are cooling steel or soup.
Important factors to consider
- Target final object(s) temperature
- The shape of the object(s)
- Specific heat of object(s) material
- Speed of travel (if moving)
- Required coverage
- Available and required cooling media flow rate
- Available liquid pressure drop across the nozzle
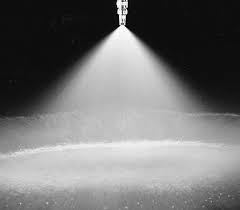

Process Gas Cooling-Spiral Nozzles / Air Atomizing Nozzles
Nozzles are used for quenching in commercial and industrial applications around the world. In many processes gas is raised to temperatures that could easily damage downstream equipment. This can either be by direct combustion, as in the case of flue gas or by secondary heating. The quickest and most effective way to cool a hot gas is through the evaporation of an injected liquid. Changing the phase of the injected liquid to gas consumes enormous amounts of energy compared to sensible/direct contact cooling. In evaporative gas cooling, a mist of water is sprayed into the hot gas. In many cases, this is flue gas from a combustion process. The water then evaporates, cooling the system rapidly as the energy is used to change the water from liquid to gas. When a volume of water is atomized into smaller droplets, more surface area is exposed, allowing the evaporation rate to increase. The rate of evaporation is often criticized as the gas must reach its final temperature before a fixed point downstream. The evaporation rate is dependent on the droplet size, temperature differential, and partial pressure among other variables.
Important factors to consider:
- Initial/final process gas temperatures
- Process gas composition (including initial water content)
- Available residence time for droplet evaporation
- Available and required flow rate
- The available pressure drop across the nozzle
- Required coverage: Ensure complete contact/cooling of the gas stream while minimizing potential wall contact
- Required droplet size: Achieve complete or partial evaporation to obtain required cooling.
- Required nozzle material: Quench nozzles often require special materials to withstand the high temperature and corrosive environments present in these applications.

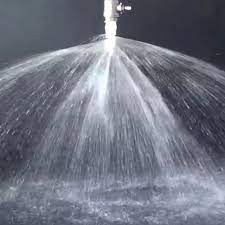
Pond Cooling-Spiral Nozzle
Cooling ponds are used to lower water temperature through contact cooling with the surrounding air. Static ponds often have low cooling efficiency and require a lot of space as only the surface of the pond is in direct contact with the air, resulting in relatively expensive use of valuable land. Spray Nozzles Online offers a wide variety of spray nozzles which can dramatically lower the expense and footprint of cooling ponds. By spraying and atomizing the water from the cooling ponds into the air, spray nozzles significantly increase the surface area of water exposed to the air, thus improving the cooling efficiency and decreasing the area needed for the pond. In some cases, the use of spray nozzles can reduce the land required to 5% of the area needed for a static pond.
Important factors to consider:
- Environment
- Average temperatures, relative humidity, prevailing wind speeds, etc.
- Nozzle placement
- In general, spray nozzles are placed evenly around/over the pond at a height that maximizes residence times while taking droplet drift due to wind into account
- Nozzle clog resistance
- Available and required flow/cooling rates
- Available pressure drop (∆P) across the nozzle
- ∆P = supply pressure at nozzle inlet – process pressure outside nozzle
- Typical operating pressures range from 10-20 PSI (0.7-1.4 bar) to produce a drop size capable of efficient cooling while minimizing evaporation losses and wind drift
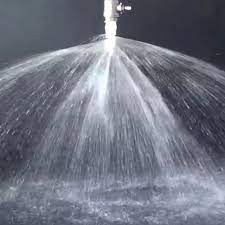
Nozzle for cooling application
Drinks cooling
Before electrostatic precipitation cooling and humidifying
Plastic pipe forming
Skin coverage wire elongation project
Draper-type muller cooling
Wire stretch project cooling
Spiral condenser cooling
Conveyor belt cooling
Chamber at kiln back end cooling
Die casting cooling
Heat treatment before quenching
Storage tank cooling
PVC pipe extrude cooling
Roof cooling
Chamber at kiln back and cooling
Hoop rolling mill cooling
Steel continuous casting
Frequently Asked Questions
In gas-cooling systems, a cool gas is passed over the worker’s body. Because gases do not typically have a large specific heat capacity, removing a large amout of heat requires a high flow rate.
Gas coolers are a part of a typical fuel system on many non-electronic engines in facility equipment. The function of a gas cooler is to cool the heated fuel return flow and realize the purpose of why excess heat needs to be removed from a system.
- Long functional life
- High performance
- Optimum quality
- Gas cooling system producing semi-fine fog.
- Can be integrated as an improvement to existing gas cooling tower facilities or incorporated when designing and building new gas cooling towers.
- Optimization of gas flow.
- Does not create problems related to unvaporized-water drainage, dust adhesion, etc.
- quantity of gases is not increased
- an investor may use recovered heat (heated up agent is clean since it has not contact with dusted process gases)
- in the exchanger there takes place a preliminary stage of de-dusting of cooled down gases
- automatic cleaning of pipes (removal of dusts from them)
- prevention of corrosion of elements of the exchanger ensured by cooling down air re-circulation (no temperature decrease below the dew point)
- prevention of decrease of the temperature below acid dew point by adding of sorbents into the cooled down gas before the exchanger
- possibility to erect multi-stage exchangers. For every stage materials are selected on the basis of existing temperatures
- possibility to erect specialized systems using fumes, which are cooled down in a bag filter and filtered, to re-cool the dirty gas
- Air Inlet Cooling
- Cooling Deluge
- Process Gas Cooling
- Pond Cooling
- Cooling Tower